Interstellar is an awesome movie, and the sound track is even better.
But after having listened it quite few times the original sound track, I quickly realize there is something wrong, not the loudness war, something worst: noise pickup during recording, not filtered out during mixing.
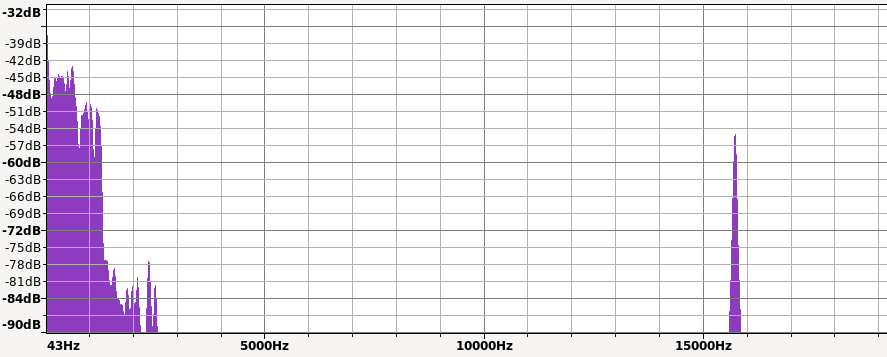
Almost the complete album is tainted, for example, in this track, “Message from Home”, is a single piano recording showing this noise standing out clearely.
Dont get me started it’s because of the MP3 or format artifact, this is present on any version, MP3, FLAC, and even on Spotify online!
Here is an extract of this sound track, do you hear it? It hurts!
If you cannot hear sounds around 16Khz, no problem, here pitched down version, to 0.5 with the noise is now at 8Khz if you don’t hear it, you may want to consult a specialist.
Because it may sound crazy that a multi million dollar movie, OST and sound track composer (Hans Zimmer) get away with this, I’ve looked up and found this reddit thread mentioning it:
Well, I’m not crazy after all and it look like it’s a Pilot Signal at “15.7342657 kHz is used to indicate the presence of MTS stereo.”
So that’s it, there is nothing to do, we are stuck with this (at least I can filter out my own version), but please, mixing engineers, next time, pay attention.
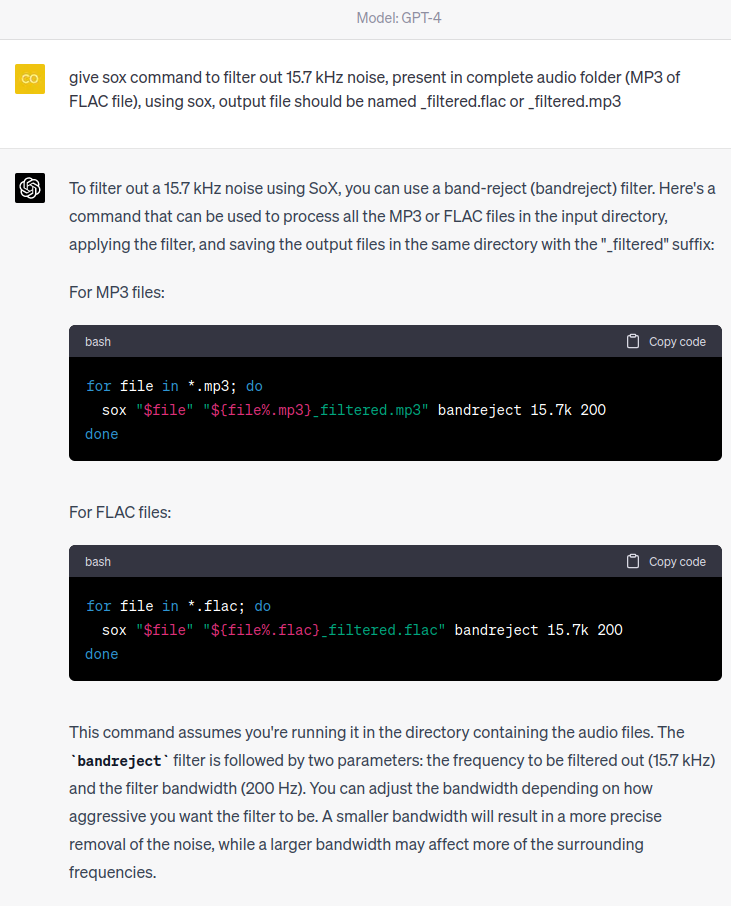